
Basically, I have now learnt if you insist on butt welding a long panel leave a small (1mm) gap between edges. I had carefully trimmed mine so they were dead tight and when I applied the weld the extra metal from the MIG caused a bulge at the join.
You can't planish (hammer) it out cause its too hard and just stretches the metal around and when you grind you end up with metal the same as a "wafer thin mint" (ask me how I know

Eventually after lots of help and advice from Mike (Metal Mickey - what a great guy


Turning to the inside I had painted the inside of the sills with epoxy primer then went over all the joins and welds with brushable seam sealer before going over the joins again with Poly Urethane seam sealer. Then also sprayed waxoyl equivalent from 3M in all the cavities. Finished article looked like this.

With everything treated internally I then took the 2 panels I had made up earlier using the carboard templates and sprayed them with epoxy primer before puddle welding into place to seal the cavity. I had also made up a new "upstand" which had rotted out on mine (Mike had said this is used to fix the side panel too). This isn't required on a camper but for completeness a new one was made up anyway


This was then puddled on top of the new top plates and the welds dressed then given a coat of etch primer.
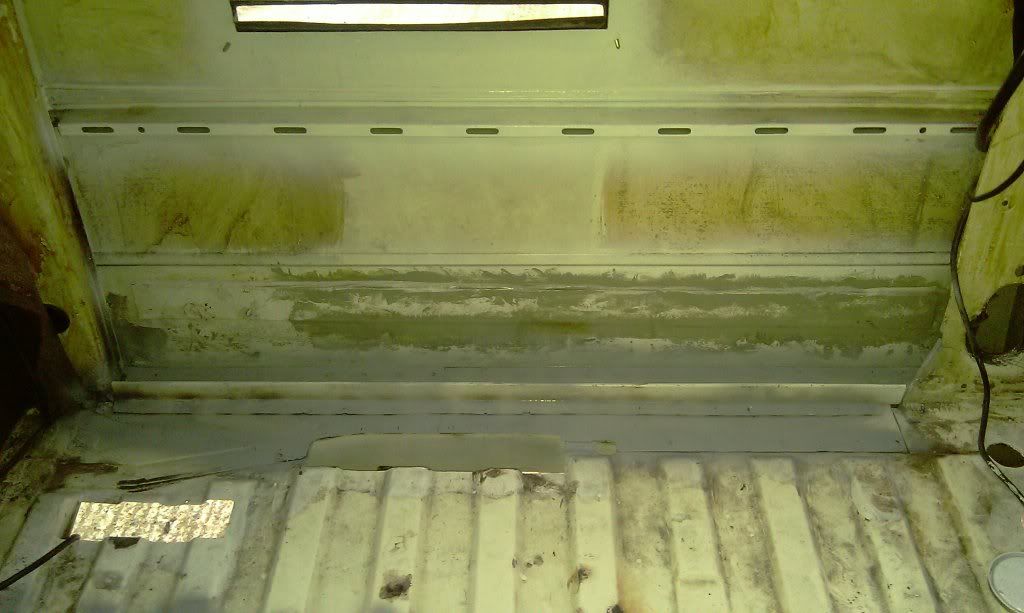
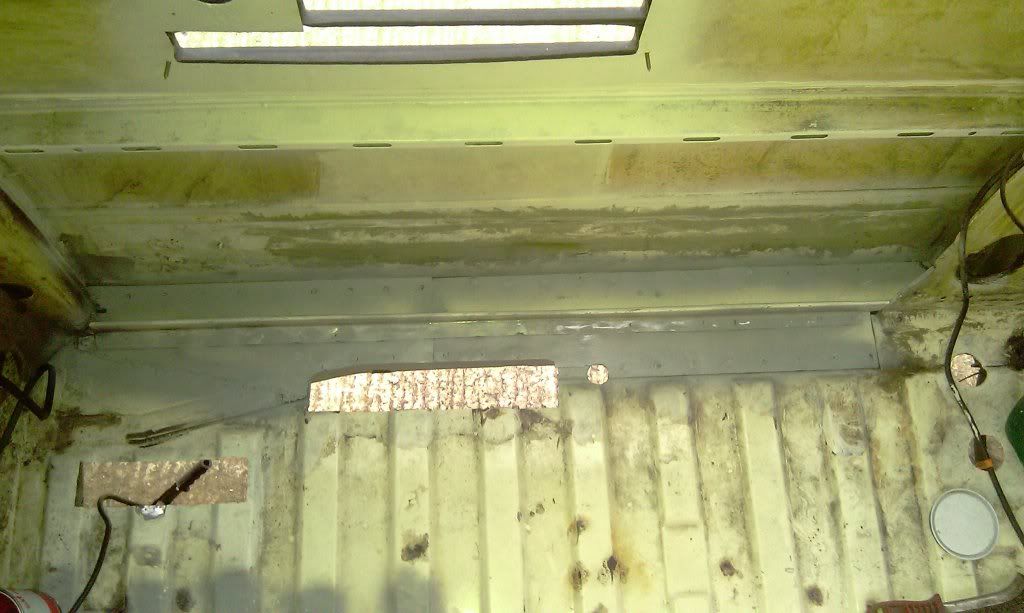
And finally, all the seams/edges are dressed in PU sealer again.
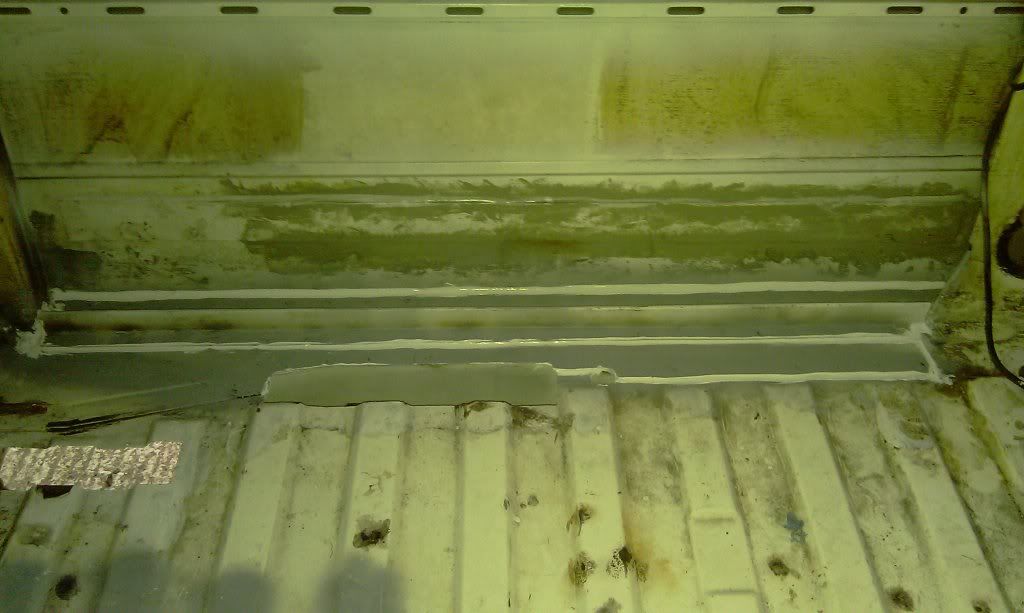
Once this has dried I will go over all the welds with brushable seam sealer just in case I have any porosity then hit the whole lot with another couple of coats of epoxy primer. Hopefuly that will keep the rust at bay for a week or two at least

MM