In a fit of ‘I’m sick of this front wheel arch’ (although it’s saving me 200 quid on a new panel) I decided to do something completely different. It also serves as a mental break for getting something achieved.
So I fitted an Omni step that I picked up cheap a while ago to stop SWMBO complaining that the Syncro is too high but not taking a loose plastic step which I hate.
So first I lined the step up retracted and extended and drilled holes in the floor.
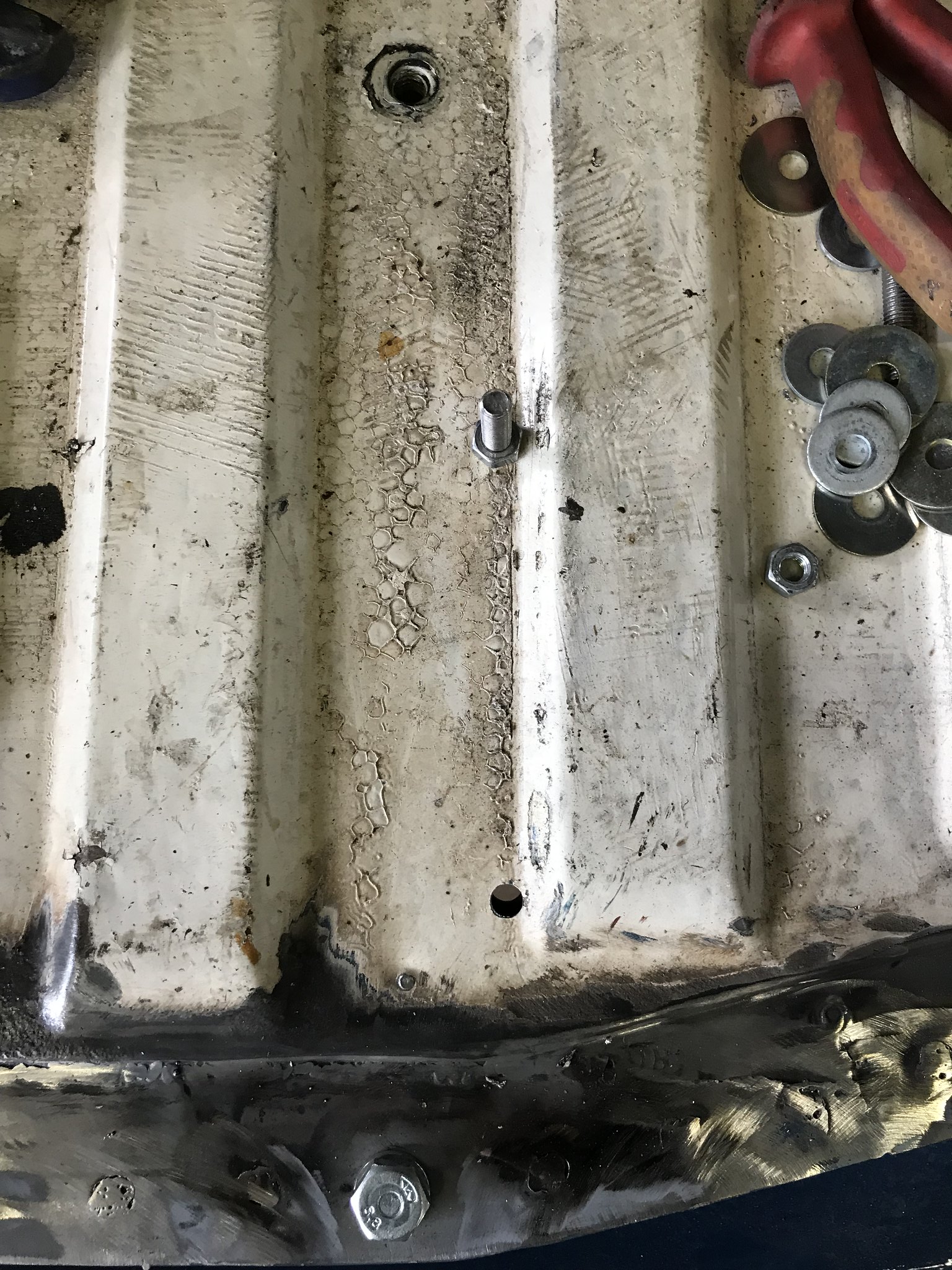
At this point I found that the floor flexed considerably even with large washers, when I say flexed I mean it started to buckle
So I found some 2mm thick box section and sliced off 8mm high sections (the height of the ridges in the floor) I took the idea from the seat belt reinforcement plates but fit it to go from the inner chassis rail to the inner sill to try and take strain off the floor. I’ll use a bit more detail because hopefully someone will learn something.
Laid on the van floor and marked from underneath for holes
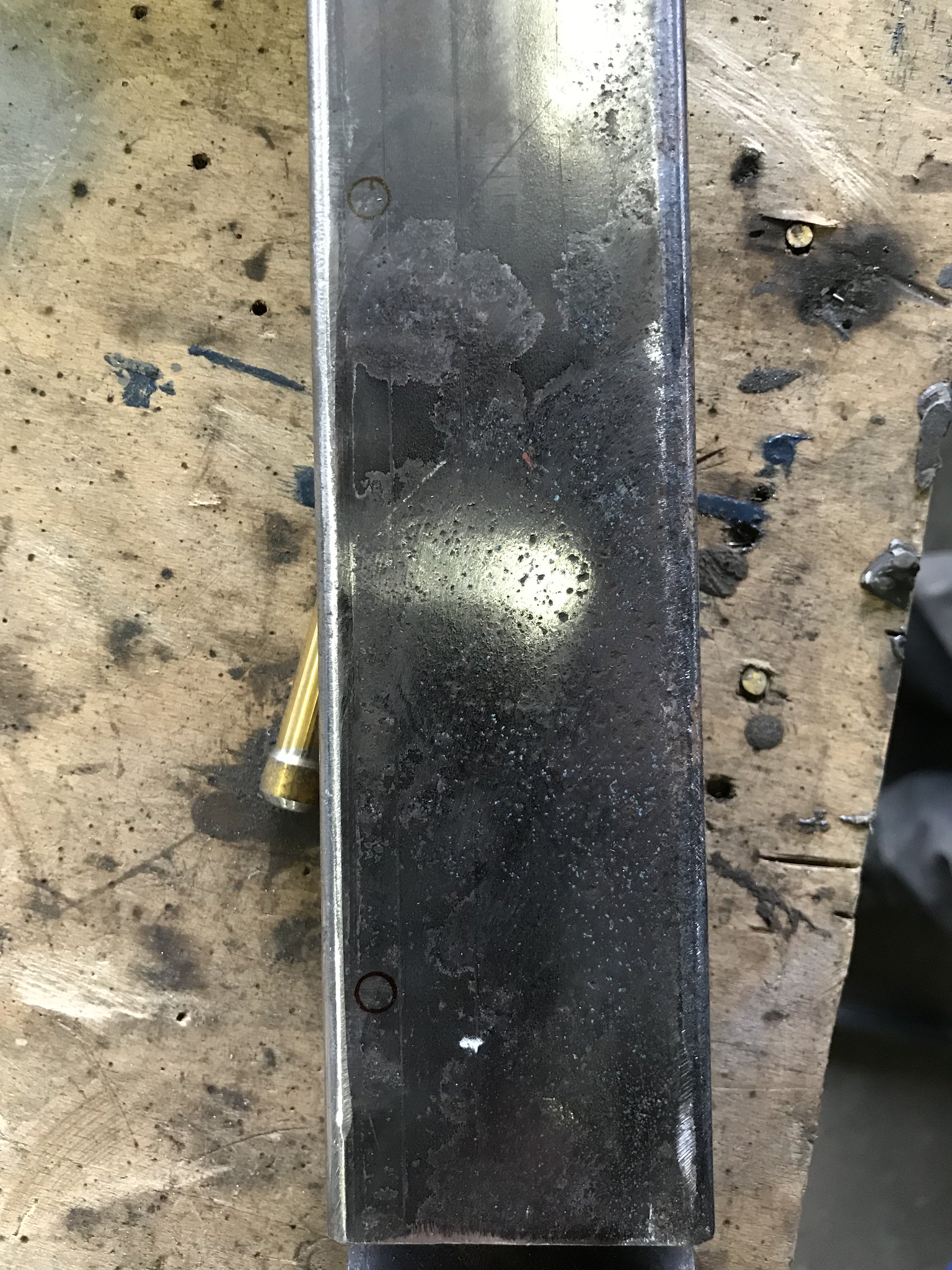
Centre punch gently to check alignment then a hefty whack to stop the drill slipping for accuracy

Then starting with a 2.5mm bit, a small hole is faster to drill and easier to correct if slightly out, using pressure to stop the drill bit blunting from running too quick. Then step up 1-1.5mm at a time to 8mm to save blunting bits and maintaining accuracy
I had to anchor the end to the inner chassis rail and most the flex is gone, once the outer sill and door channel is on it should take the last few mm out, if not I’ll seam weld the reinforcement to the floor.
Bolts welded to reinforcement to create studs for easier installation, which was deliberately sited in the gaps
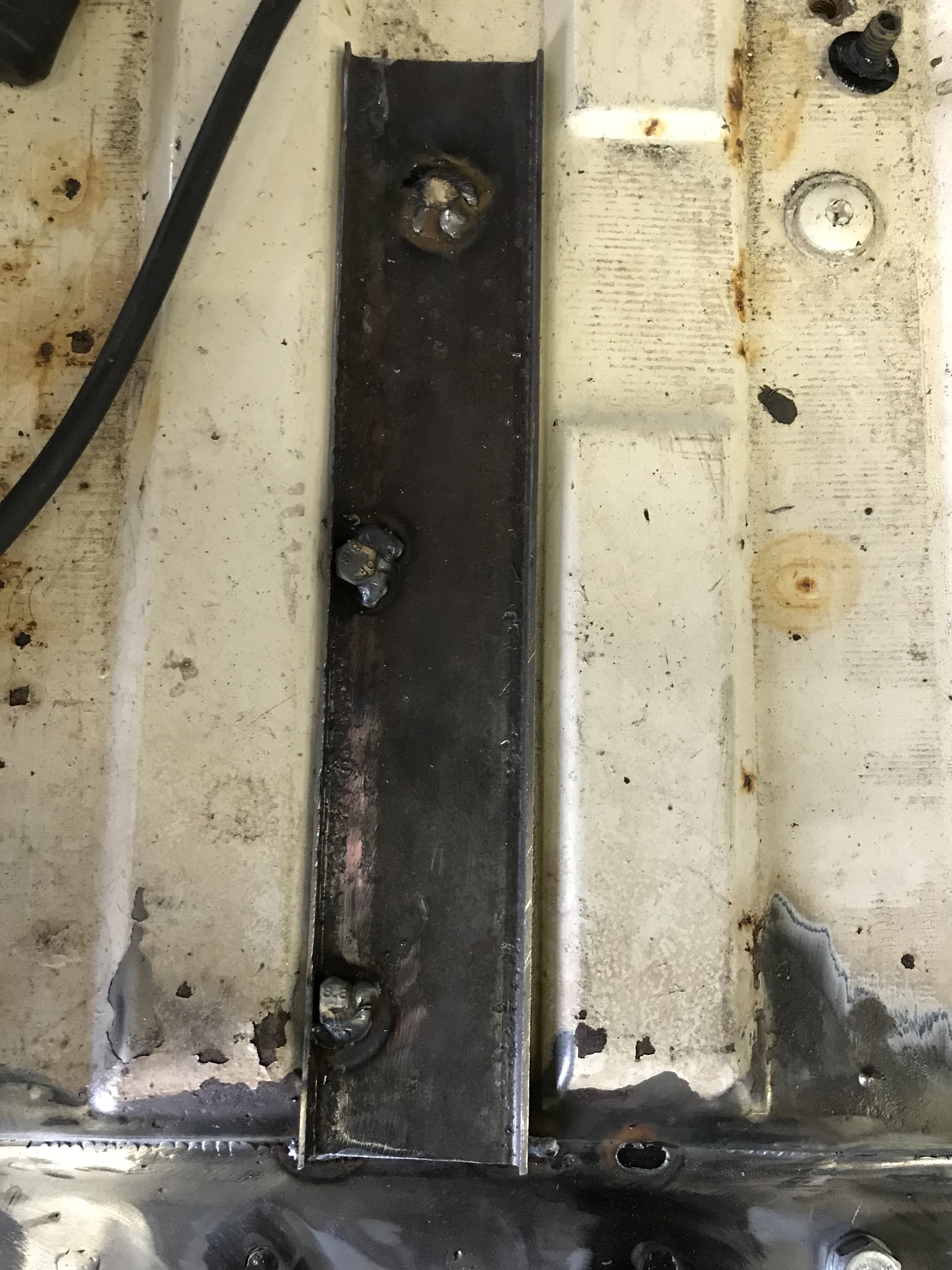
I welded the shank from a bolt onto the step frame to limit its rearward movement by a few mm and stop it hitting the inner chassis rail.
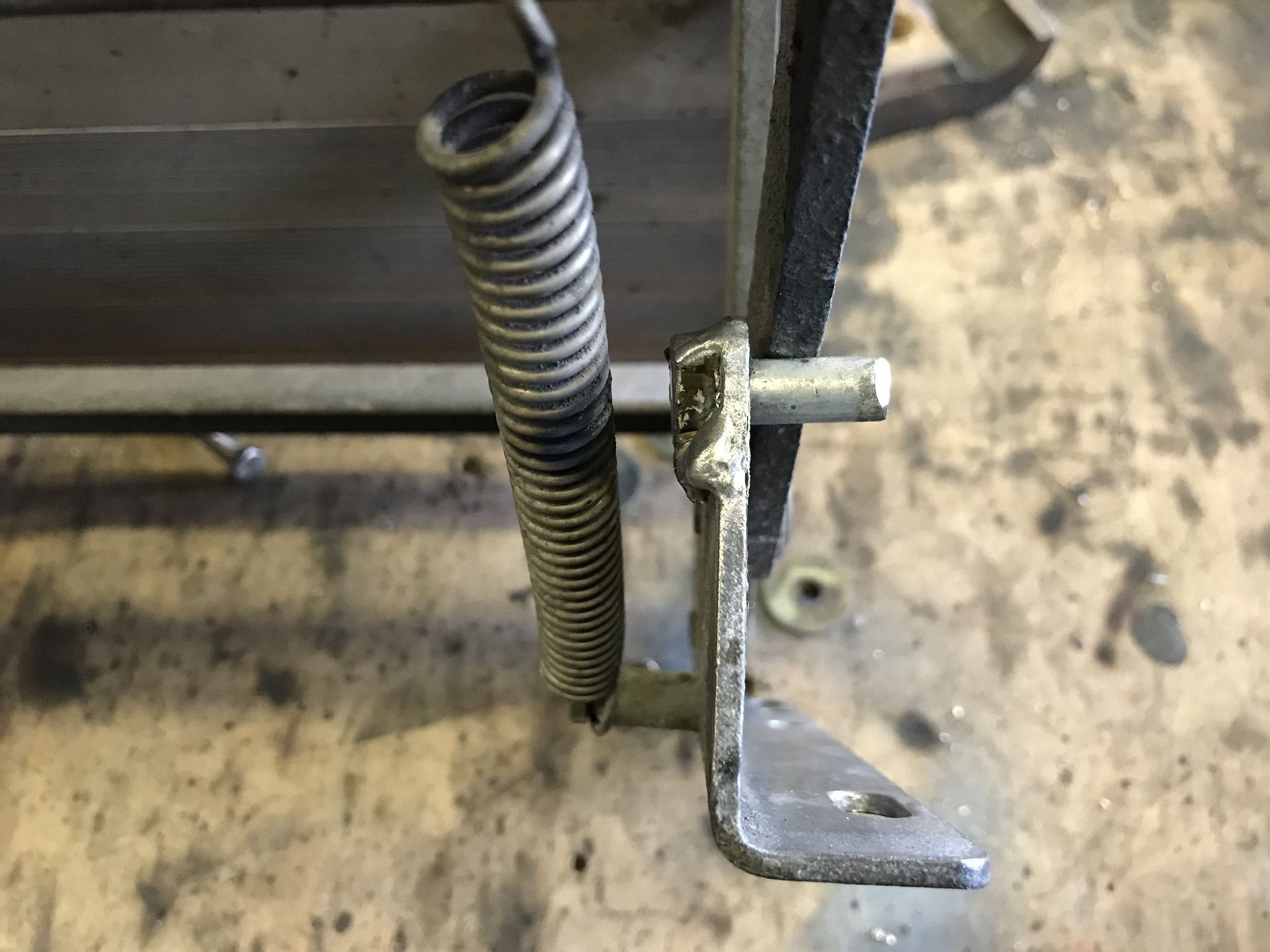
Bolted up showing clearance when retracted to the outer sill.
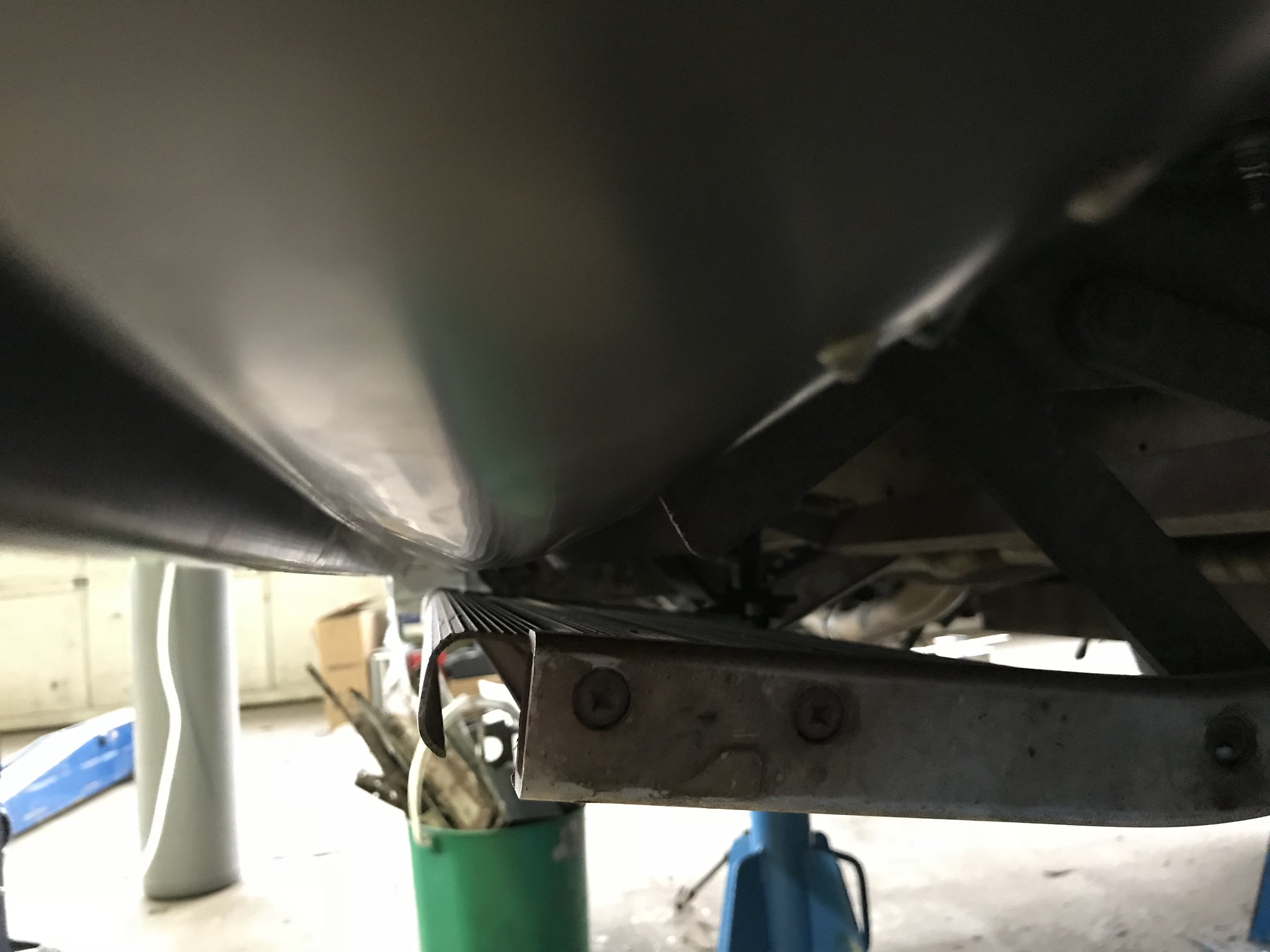
Clearance to the inner chassis rail also showing the packing washers to level the step nicely. Also showing the bolt stops that stop the step retracting too far and hitting the chassis rail before cutting and welding. The step still goes past the cam over point when retracted and remains in place.
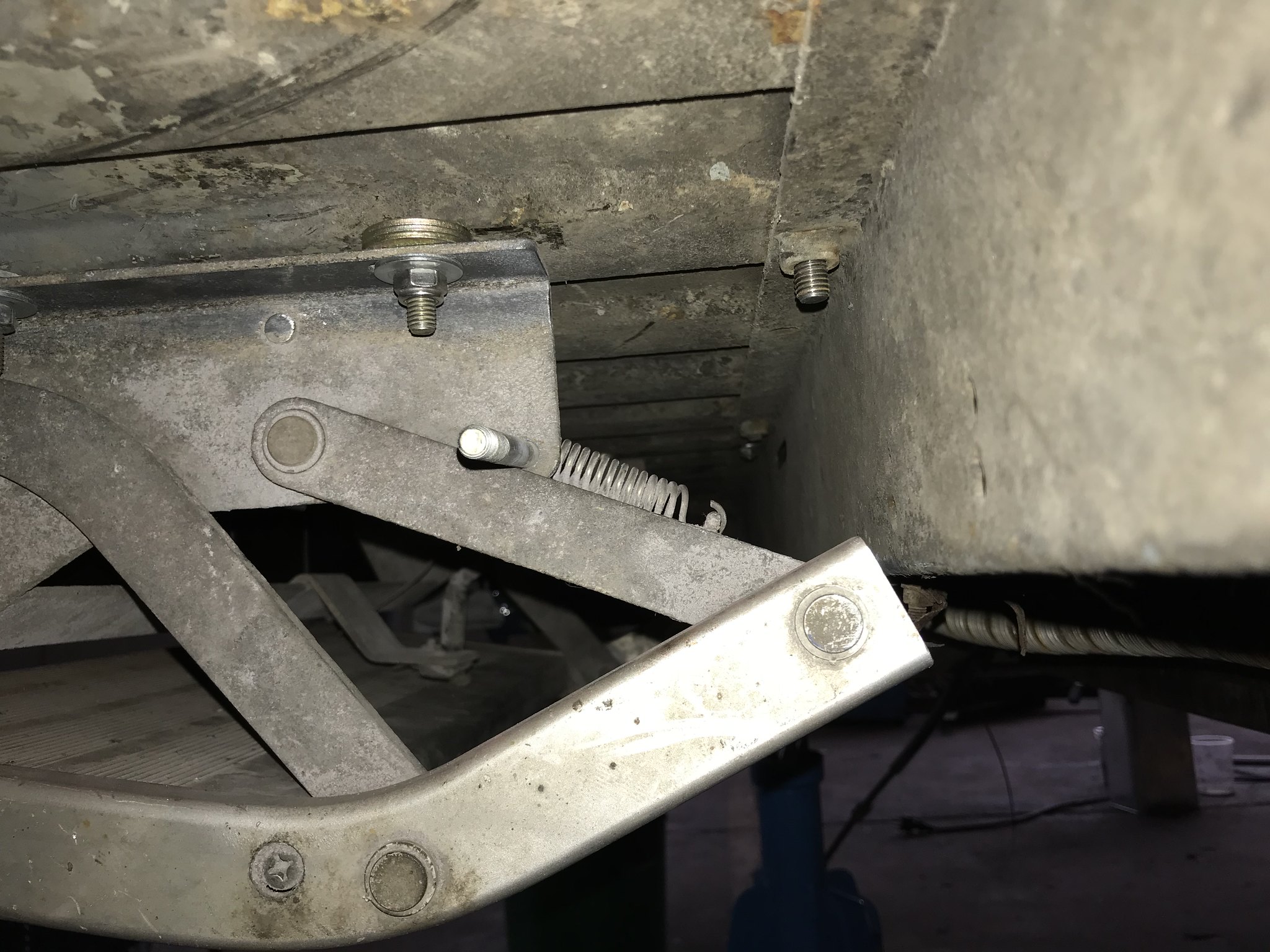
Extended, really pleased with the fit and clearance on the sill, it was proper wet finger in the air estimate from the step diagram that it would fit.

Retracted, I eventually would like rock sliders to protect my body work from trees, walls, car doors etc and these should sit fine to the step I hope.
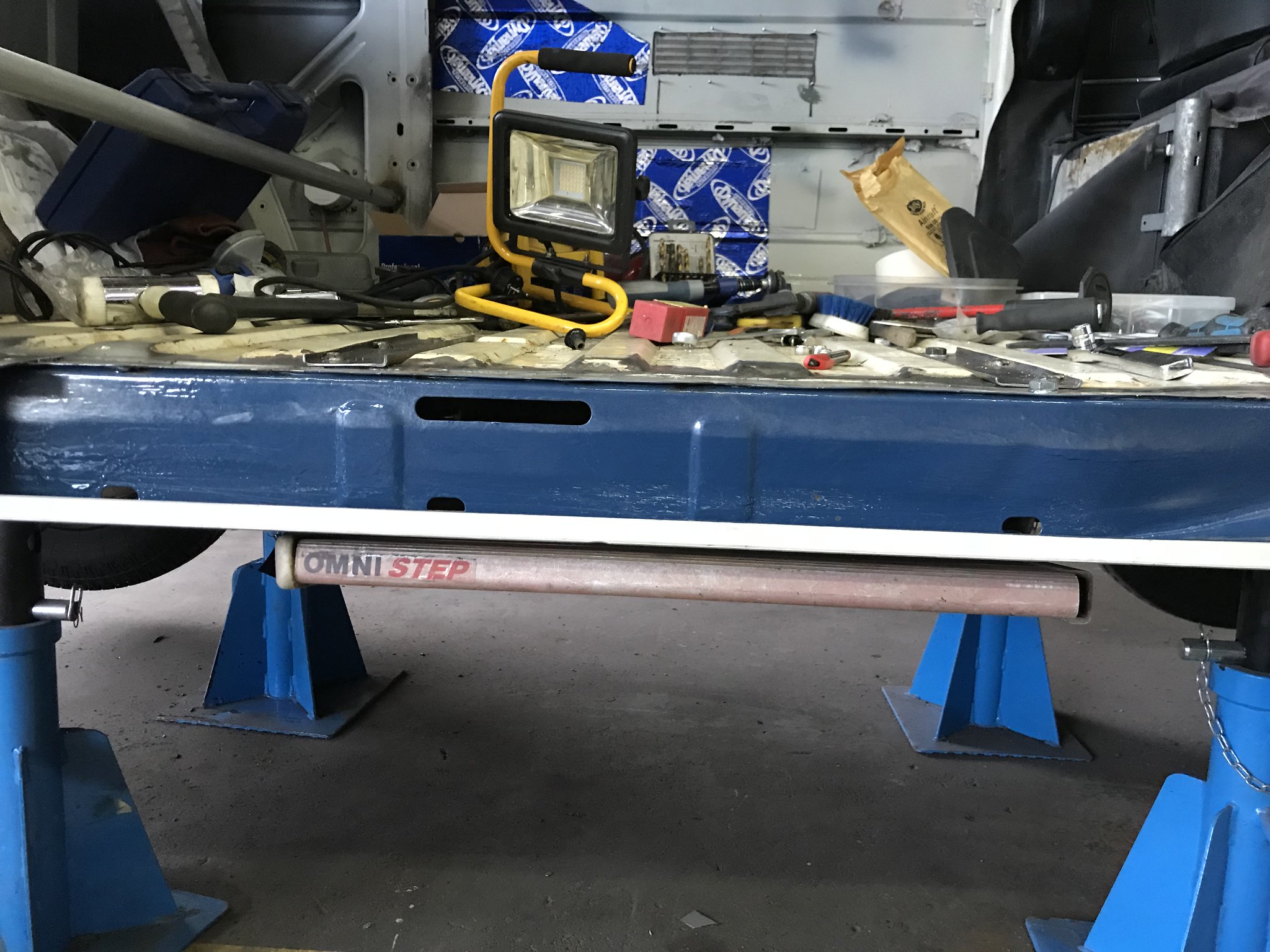
Extended

I’m really happy with this and the height is really comfortable even with the bus completely in the air on axle stands.
So completely off track, but a win for my head so I feel a bit more invigorated to continue with body work.